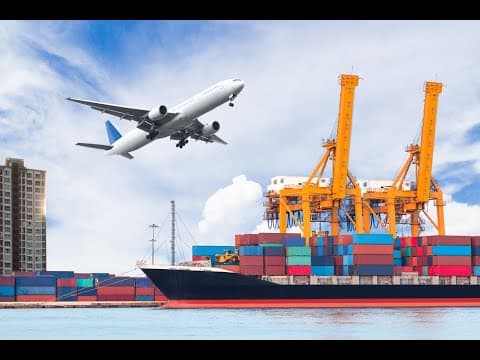
5. New Product Innovation(Part 1) - Supply Chain Management
Innovative products nowadays are highly competitive in the market!! In this video we will compare the traditional(sequential) approach with the new product development/Cross-team functioning approach in product development. Many companies nowadays have adopted the NPD/CTF approach to increase flexibility and boost innovations. What are the pros and cons of each? What are their characteristics? Which one should I adopt if I'm a manager? We will discuss and explore in this video. Course: Supply Chain Management
5. New Product Innovation(Part 1) - Supply Chain Management
New Product Innovation in Supply Chain Management
Introduction to New Product Development Approaches
- The lecture focuses on new product innovation, comparing transitional and sequential approaches in product development.
- Emphasis is placed on understanding the value lifecycle, which combines product lifecycle and new product innovation cycles.
Importance of New Product Development
- New product development is crucial for competitive advantage despite its high costs and risks.
- Companies may need to raise prices significantly to achieve profitability when launching new products.
Lead Time Definitions
- Lead time is defined as the duration from customer order to delivery, as well as the internal process from concept initiation to market launch.
- Internal lead time includes all stages within a company until a product is ready for market.
Concurrent Engineering Concept
- Concurrent engineering involves simultaneous work processes rather than sequential ones, enhancing efficiency in new product innovation.
- This approach utilizes cross-functional teams (CFT), promoting collaboration across different departments during the development process.
Comparison of Sequential vs. Concurrent Approaches
Sequential Approach Characteristics
- The traditional sequential approach separates each stage: concept, design, prototype, manufacturing, marketing, and distribution.
- Each phase must be completed before moving to the next; this can lead to inefficiencies due to lack of feedback loops between stages.
Communication Dynamics in Sequential Approach
- Communication flows forward without opportunities for revisiting earlier stages once they are completed (e.g., concept cannot be altered after passing it to design).
New Product Development Communication Challenges
Design and Prototype Limitations
- The design team and prototype team face a lack of flexibility, as once designs are finalized, there is no opportunity for revisions or remakes.
- The communication structure is primarily upward, which can lead to disadvantages such as increased costs and chaotic coordination when new concepts arise.
- If the prototype fails during manufacturing, it incurs additional costs due to the need for redesign and re-prototyping.
Advantages and Disadvantages of Upward Communication
- While upward communication saves time and reduces chaos within the company, it limits feedback loops that could improve product development.
- The sequential approach in project management may hinder adaptability, leading to potential drawbacks in innovation.
Flexible New Product Development Approach
Project Lead Time Dynamics
- Project lead time measures the duration from concept initiation to market launch; understanding this timeline is crucial for effective planning.
- A flexible NPD approach can lower lead times but may also result in longer durations if new designs are required due to initial failures.
Concurrent Engineering Benefits
- Concurrent engineering allows different teams (design, prototype, manufacturing) to work simultaneously, potentially speeding up the process but also complicating coordination.
- This method enables real-time feedback between teams, allowing for adjustments based on ongoing developments rather than waiting until later stages.
Feedback Mechanisms in NPD
Importance of Backward Communication
- In an NPD framework with backward communication, teams can provide feedback on concepts and designs that facilitate iterative improvements.
- If prototypes fail or cannot be manufactured effectively, design teams can revise their approaches based on practical insights gained during production trials.
Market Testing Strategies
- Marketing efforts are essential after product launches; if a product does not perform well in the market, design teams must pivot quickly to develop alternatives.
Understanding Risk Exposure in Product Design
The Importance of Design Flexibility
- New designs are created daily, allowing the design team to quickly pivot if a product fails in the market, providing manufacturers with alternative options.
- The "risk exporter period" refers to the potential risks incurred once a product reaches the design stage, marking a critical point where changes become difficult.
- In sequential approaches, risk exposure begins at the design stage; however, flexible methodologies allow for adjustments during marketing stages, reducing overall risk.
Challenges of Sequential Approaches
- A significant issue in sequential approaches is "concept freeze," which occurs when manufacturing reveals flaws after design and prototyping are complete.
- If manufacturing encounters issues post-design phase, it may necessitate restarting from concept development, leading to wasted time and costs.
Advantages of Flexible Methodologies
- In contrast to sequential methods, flexible approaches enable concurrent work by design teams and manufacturers, facilitating quicker adaptations if problems arise during production.
- This simultaneous workflow reduces risk exposure since feedback can be integrated throughout various stages of product development.
Communication Dynamics in Different Approaches
- Sequential approaches rely on one-directional communication which can be risky as customer preferences evolve without room for adjustment.
- External costs may accumulate if products fail to resonate with consumers after extensive investment in research and development.
Evaluating Pros and Cons
- While sequential methods offer simplicity and clear accountability, they also present higher risks due to limited adaptability.
- Flexible methodologies provide multiple functions working simultaneously but may introduce complexity that could lead to increased costs depending on circumstances.
Balancing Lead Time and Market Needs
- Traditional approaches simplify processes but might lack problem-solving capabilities compared to more dynamic strategies that adapt over time.
- Although flexible methods may extend lead times due to iterative testing (e.g., trying multiple products), they ultimately aim for better alignment with customer preferences through ongoing adjustments.
Enhancing Problem-Solving Capabilities
- Increased lead times can indicate thorough product development aimed at meeting market demands effectively while enhancing problem-solving capabilities through continuous feedback loops.
Understanding Coordination Costs in Concurrent Engineering
The Impact of Concurrent Engineering on Coordination Costs
- The implementation of more ideas in concurrent engineering leads to increased coordination costs due to simultaneous processes across departments.
- In the CFG approach, all teams must collaborate until the final product is ready for market, resulting in higher coordination demands and potential waste from duplication of efforts.
- The trial-and-error nature of product development can lead to material waste and financial losses, creating chaos within the company if not managed properly.
Challenges and Risks Associated with Concurrent Engineering
- Chaos during concurrent engineering can significantly reduce efficiency, potentially leading to worse outcomes than traditional sequential approaches.
- New companies may struggle with implementing a successful CFT (Concurrent Functional Team) approach due to difficulties in achieving efficient inter-departmental collaboration.
Learning from Mistakes and Employee Morale
- Companies must learn from their mistakes; experience over time can help manage the CFT approach effectively.
- Employee morale may decrease during chaotic processes, particularly in less established companies compared to industry giants like Microsoft or Apple.
Advantages and Disadvantages of CFT vs. Traditional Approaches
- While CFT has its advantages, it also presents challenges such as decreased employee enthusiasm and commitment due to exhaustion from high coordination demands.
- Traditional approaches often result in longer lead times and higher risk exposure; this is why many companies are shifting towards CFT despite its complexities.