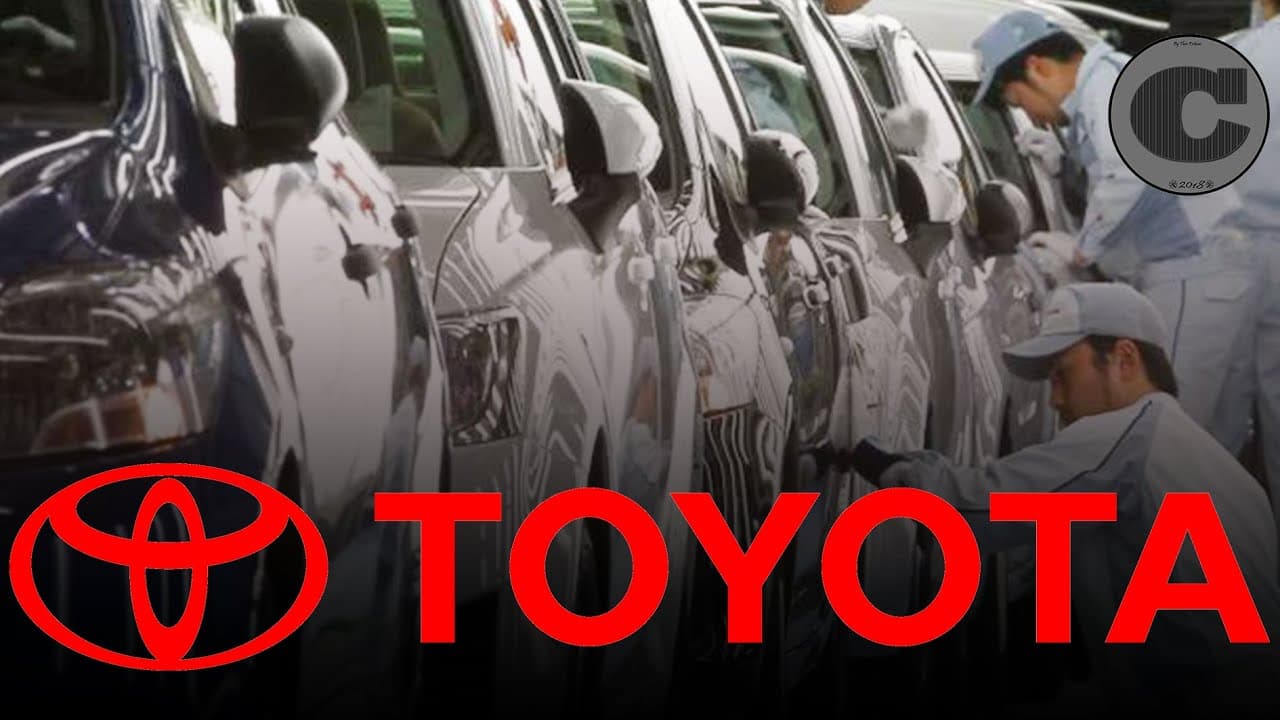
Le Toyotisme | 3 minutes de culture #45
Le Toyotisme est une forme d'organisation du travail, de la production, ... qui a comme principes les 5 zéros, la différenciation retardée, les cercles de qualités, la kanban, kaizen ,... Le Toyotisme a vu le jour chez Toyota grâce à son inventeur l'ingénieur japonais Taiichi Ōno. Instagram : 3minutesdeculture Site internet : 3minutesdeculture.fr Mes principales sources : -La Bande Dessiné "Economix" écrite par Michael Goodwin et illustrée par Dan E.Burr aux éditions "Les Arènes" -Cours gestion de stock DUT Gestion Logistique et Transport 2nd année -Wikipédia en général : https://fr.wikipedia.org/wiki/Toyotisme#:~:text=Le%20toyotisme%20est%20une%20forme,n'est%20pas%20appliqu%C3%A9e%20imm%C3%A9diatement. -Bulsuk : https://www.bulsuk.com/p/the-toyota-production-system.html
Le Toyotisme | 3 minutes de culture #45
Introduction to Toyotism
The introduction discusses the concept of Toyotism, an organizational work structure developed by a Japanese engineer named Taisho in Toyota during the second half of the 20th century. It contextualizes Japan's post-World War II situation due to resource scarcity and the need for economic revival.
Development of Toyotism
- Japan faced resource scarcity post-WWII, leading to heavy reliance on imports like coal, natural gas, and oil.
- To overcome resource deficits, Japan focused on industrial development leveraging its population and investing heavily in industries for a competitive advantage.
Principles of Toyotism
- Toyotism emerged as a solution for enhanced production efficiency amidst changing contexts like market saturation and demand complexities.
- Key principles include Just-in-Time production, quality focus, cost reduction, and waste minimization.
Key Elements of Toyotism
This section delves into the core elements that define Toyotism as a modernized and ethical approach to production management.
Core Principles
- Emphasis on non-wastage, quality improvement, reduced lead times, and cost optimization benefitting consumers with better products and innovations.
- Implementation includes zero defects, zero delays through streamlined production processes emphasizing worker responsibility and versatility.
Impact on Work Culture
Discusses how Toyotism revolutionized work culture by empowering workers with responsibilities and fostering employee engagement.
Work Culture Transformation
- Shift towards worker consultation via quality circles led to increased employee motivation in Japanese automotive industries compared to American counterparts.
- Workers viewed as valuable assets rather than mere machines under this system promoting productivity through intrinsic motivation beyond monetary incentives.
Tools Used in Automotive Industry
Explores specific tools employed in the automotive sector influenced by Toyotism principles for operational efficiency.