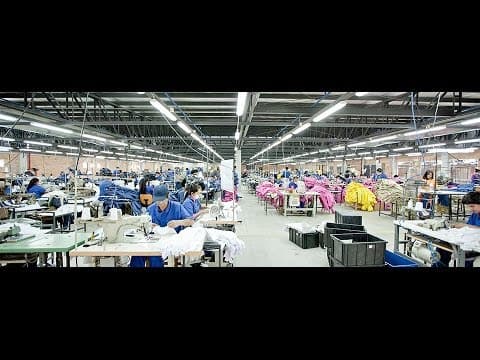
SELLO NACIONAL8 - Blue Desing America - Fabrica de Jeans
Visitamos a BLUE DESING AMERICA, una impresionante fábrica de Jeans paraguaya de alta tecnología, que fabrica mas de 9.000 unidades por mes, constituyéndose ademas, en la segunda empresa en el país en contar con la Certificación LEED (empresa sustentable), y la única planta de Latinoamérica que la posee. Con maquinarias de ultima generación, te mostramos los procesos de fabricación de inicio a fin, con los mas pequeños detalles, incluyendo una Planta de Tratamiento de efluentes ultra moderna. Nuestro agradecimiento a Jorge Bunchicoff por abrir sus puertas a SELLO NACIONAL.
SELLO NACIONAL8 - Blue Desing America - Fabrica de Jeans
Blue Design America: Leading Denim Production in Paraguay
Overview of Blue Design America
- Blue Design America is recognized as the leading company in denim development, production, and exportation in Paraguay, serving as a reference for many brands across South America.
- The company produces over 9,000 jeans monthly and is noted for its technological advancements in manufacturing.
LEED Certification and Sustainable Practices
- Blue Design America was built with special standards to achieve LEED certification, which focuses on energy efficiency and sustainable design. This certification is awarded by the U.S. Green Building Council.
- The facility utilizes innovative energy-saving methods such as using ambient heat for water heating, significantly reducing energy consumption.
- Only two buildings in Paraguay hold LEED certification: BBVA's building and Blue Design America’s factory, making it the only denim factory in Latin America with this distinction.
Water Treatment and Environmental Compliance
- The company has established a wastewater treatment plant that aims to recycle up to 80% of laundry water, adhering to both Paraguayan regulations and stricter European standards.
- The treatment process includes recycling water from bathrooms for irrigation purposes, showcasing their commitment to environmental sustainability.
Production Process Insights
- Collaboration with clients is essential; designs are often created together during visits or through proposals made by Blue Design America's team.
Production Process of Jeans
Overview of the Production Area
- The production area includes a space for creating samples and prototypes, which is the second step after making molds. Here, only one garment is cut to develop the sewing system.
- This section is crucial as it determines how garments will be washed, including the duration and types of chemicals used to achieve desired colors.
Importance of Laboratory Testing
- The facility has advanced technology that allows for extensive testing; few laboratories in Latin America have such capabilities.
- Unlike typical laundries where samples are produced alongside mass production, this lab conducts specific tests on individual samples to ensure quality standards.
Design and Distressing Techniques
- There’s a significant amount of trial and error involved in achieving the right color and distressing effects on jeans.
- A colleague specializes in creating wear patterns on jeans meticulously, generating various shades and distress marks to give a vintage look.
Finalizing Designs Before Washing
- The initial fabric starts darker but undergoes processes that lighten it while maintaining a natural appearance as if worn over time.
- After designs are finalized, they move to washing where colors are set based on pre-established marks created during design.
Washing and Finishing Processes
- The intensity of distressing must be carefully controlled; excessive damage can ruin the garment.
- Following manual preparations, garments proceed through washing, drying, and sometimes heat treatment at high temperatures to set resins that create permanent wrinkles or shine.
Raw Materials Acquisition
Overview of Denim Fabric Manufacturing Process
Sourcing and Storage of Raw Materials
- The company collaborates with manufactura Pilar for denim production, sourcing additional fabrics globally from key suppliers in Turkey, Pakistan, and India, which are known for their significant denim manufacturing capabilities.
- Raw materials are stored in a specially designed warehouse that maintains optimal light and humidity conditions to prevent damage; exposure to sunlight or excessive heat is strictly avoided.
Quality Control Measures
- Initial quality control involves inspecting each roll of fabric for defects using a specialized machine where operators mark any imperfections. This step is crucial for ensuring high-quality raw materials.
- Fabrics containing elastane or stretch fibers must rest for 12 to 24 hours after inspection to manage shrinkage effectively, emphasizing the importance of this resting period in the production process.
Production Workflow
- Once fabrics have rested and passed quality checks, they are transported via an elevator to the next stage of production on the first floor.
- The layout follows the Toyota Production System, promoting efficiency as materials move through a U-shaped workflow back to the second station.
Product Development and Cutting Process
- The product development phase begins with creating prototypes based on specific designs; this includes developing molds that dictate styles such as fitted or loose pants.
- A computer-operated system automates fabric cutting, optimizing material usage compared to manual methods commonly used in other factories.
Sewing Preparation and Organization
- After cutting, parts are labeled according to sizes before being sorted into baskets. This organization is essential for subsequent processes like embroidery.
- Each sewing cell operates under the Toyota method, allowing complete garment assembly within designated groups. This structure enhances productivity while maintaining strict quality control measures.
Efficient Distribution System
- Cut pieces are organized into boxes containing 20 units each, facilitating streamlined distribution among sewing cells.
Production Process of Jeans
Overview of the Sewing Cell
- The team is heading to sewing cell two, where boxes are managed based on production needs. Operators monitor supply levels to ensure continuous operation.
- Each cell aims to produce approximately 100 garments per hour, with a workflow that allows fabric cuts to circulate through the entire cell until completion.
Laundry and Distressing Techniques
- Garments are sent down a chute to the laundry, marking the beginning of a new production process focused on manual distressing techniques.
- Artisanal methods are employed for creating specific wear patterns like "whiskers" and tears in jeans, showcasing craftsmanship in denim finishing.
- A laser machine represents an automated version of these artisanal processes, capable of replicating intricate designs at high speed while maintaining quality.
Automation in Denim Production
- The latest laser technology standardizes production and enhances efficiency without compromising the natural look of distressed jeans.
- Graphic designers create digital mock-ups for distress patterns which are then executed by machines, ensuring precision in each garment produced.
Innovations in Washing Techniques
Importance of Experience and Machinery
- The facility emphasizes its unique washing capabilities as a differentiator from other manufacturers; experience plays a crucial role alongside advanced machinery.
- Italian and Spanish machines (e.g., Tonello brand), known for their automation and eco-friendliness, handle large volumes while ensuring consistent results.
Chemical Processes in Denim Treatment
- Raw denim undergoes washing with stones and chemicals to achieve desired color variations ranging from dark blue to white.
- Pre-washing techniques have evolved since the 1970s, allowing for sophisticated contrasts that mimic vintage styles effectively.
Environmental Considerations
Water Treatment Processes
- The plant produces significant wastewater due to extensive water use during distressing. Two types of wastewater are generated: one containing dyes and another with basic blue hues.
Overview of Water Treatment Processes
Biological Treatment Phase
- The initial stage involves a chamber designed to treat wastewater, specifically targeting blue water that requires different treatment methods.
- This chamber utilizes specific bacteria that consume the blue color from the water, effectively oxygenating it and creating bubbles as a result of this biological process.
Filtration Process
- Following the biological treatment, the water is passed through two stages of filtration using activated carbon filters to further purify it.
- After passing through the carbon filters, a chemical process is applied in a third stage to remove any remaining blue coloration from the water.
Finalization and Quality Control in Production
Finishing Touches on Garments
- Once garments are dried, they undergo final assembly where buttons, rivets, and labels are attached—especially those damaged during washing processes.
Quality Assurance Measures
- A comprehensive quality control system ensures 100% inspection of all production items before packaging. Each section has its own quality checks followed by an overall audit.
- The quality department functions like an auditing body; each production area is responsible for maintaining its own standards while also being subject to external verification.
Specific Quality Checks
- Different sections focus on distinct aspects of quality; for instance, laundry checks concentrate solely on washing outcomes rather than sewing details which are handled separately.
Visual Inspection Importance
- The final inspection relies heavily on visual assessments rather than advanced technology. Personnel require extensive training to accurately evaluate garment quality.
Conclusion and Acknowledgments
Exporting Products
- After completing all processes, the final steps involve exporting products and managing financial transactions related to sales.